Unlocking Excellence in Injection Mold Tool Design: Insights from Leading Metal Fabricators
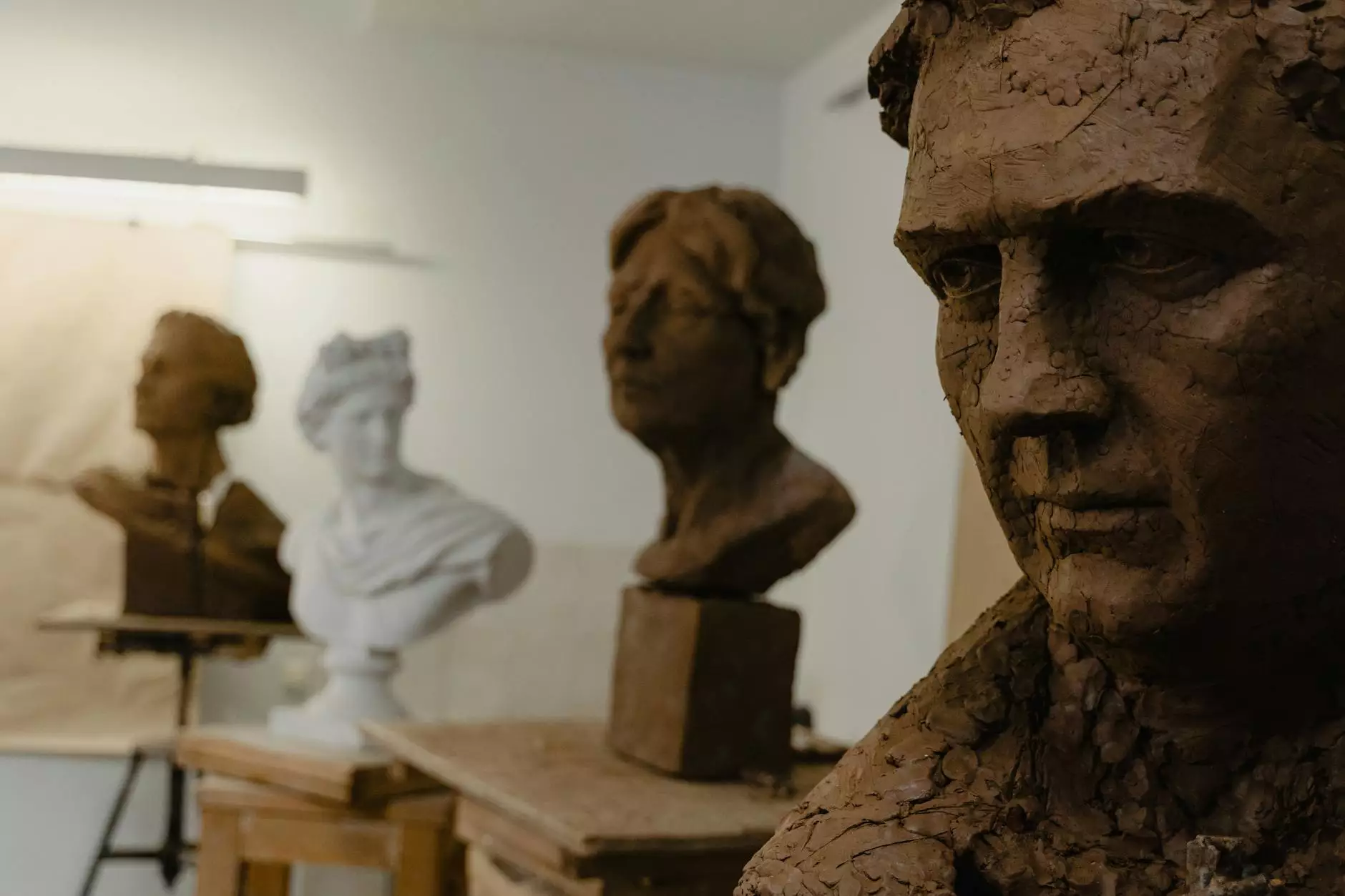
In the competitive world of manufacturing, precision engineering and cutting-edge technology are vital for success. Among the many facets of modern production, injection mold tool design stands out as a cornerstone for creating high-quality plastic components efficiently and reliably. Leading metal fabricators, such as those found at deepmould.net, have pioneered innovative strategies to enhance the precision, durability, and cost-effectiveness of injection molds. This comprehensive guide delves deep into the art and science of injection mold tool design, providing invaluable insights for manufacturers, engineers, and businesses striving to excel in the injection molding industry.
Understanding the Fundamentals of Injection Mold Tool Design
At its core, injection mold tool design is a meticulous process that transforms a conceptual product into a tangible, functional mold. This process involves multiple phases—each critical to the final product's success. A deep understanding of the underlying principles ensures that the mold is not only precise but also durable and efficient.
Key Components of Injection Molds
- Main Body (Cavity and Core): Forms the shape of the final product. Usually made from hardened steel or aluminum depending on application requirements.
- Runner System: Channels that direct molten material into the cavities.
- Sprue and Gates: Entry points for the molten material into the cavity, designed for optimal flow and minimal defects.
- Ejector System: Components that remove the finished part without damage.
- Cooling System: Channels that regulate temperature for consistent part quality.
The Importance of Precision in Injection Mold Tool Design
Precision is the foundation of high-quality injection molding. The injection mold tool design directly impacts the dimensional accuracy, surface finish, and overall consistency of the produced parts. Manufacturers often invest significant resources into refining their design processes to minimize defects such as warpage, short shots, or sink marks.
Designing for Tolerance and Repeatability
Achieving tight tolerances requires meticulous planning and execution. Advanced CAD/CAM software enables designers to simulate the mold's performance under various conditions, ensuring that every cavity maintains consistent dimensions. Repeated high-quality production relies heavily on this repeatability, which is rooted in the robustness of the initial injection mold tool design.
Innovative Techniques in Injection Mold Tool Design
Modern tools and methodologies have revolutionized how metal fabricators approach injection mold tool design. The integration of technological advancements ensures molds are not just functional but optimized for efficiency and longevity.
Computer-Aided Design (CAD) and Simulation
CAD software enables designers to create highly detailed mold models. Simulation tools predict how molten plastic will flow, cool, and eject, allowing for optimization before physical production. This reduces prototyping costs and accelerates time to market.
Rapid Prototyping and 3D Printing
Rapid prototyping techniques allow for quick testing of injection mold tool designs. 3D printing enables the fabrication of mold components or prototypes for testing, identifying potential issues early and iterating designs swiftly.
Utilizing High-Performance Materials
The choice of materials for mold manufacturing is critical. Modern metal fabricators leverage materials like P20 steel, H13 tool steel, or even diamond-like coatings to increase the durability and lifespan of molds, especially for high-volume or demanding applications.
Design Strategies for Enhancing Mold Durability and Efficiency
An effective injection mold tool design balances material properties, geometry, and manufacturing techniques to create molds that stand the test of time. Here are essential strategies employed by top-tier metal fabricators.
Optimizing Mold Geometry
Designing for optimal flow and ejection involves complex calculations to prevent common issues such as weld lines, hot spots, and excessive wear. Using conformal cooling channels and smooth taper angles helps in achieving uniform cooling and easy ejection, thereby extending mold lifespan.
Modular Mold Design
Modular components facilitate easier maintenance and facilitate quick modifications for different product variants. Modular design also simplifies repairs, reducing downtime and overall costs.
Advanced Surface Treatments
Surface treatments like nitriding or diamond-like carbon (DLC) coatings enhance wear resistance and reduce corrosion. This is especially useful for molds that operate under high-pressure, high-temperature conditions, ensuring sustained precision over extended production runs.
Cost Optimization in Injection Mold Tool Design
Balancing cost and performance is a perpetual challenge. Industry-leading metal fabricators employ a variety of cost-effective techniques without compromising quality. Here are some of the strategies:
- Design for Manufacturing (DFM): Streamlining designs to be easier and less costly to produce.
- Standard Part Utilization: Incorporating off-the-shelf components when possible to reduce lead time and expense.
- Energy-Efficient Manufacturing: Using CNC machining and EDM processes that minimize material waste and energy consumption.
- Outsourcing High-Precision Machining: Partnering with specialized metal fabricators for complex components ensures quality while controlling costs.
Collaborating with Expert Metal Fabricators for Superior Injection Mold Tool Design
Achieving top-tier injection mold tool design requires collaboration with experienced metal fabricators. Partnering with a business like deepmould.net, known for their expertise in metal fabrication and custom molds, can significantly benefit your manufacturing processes.
Expert fabricators offer:
- Professional consultation during the concept and design phases
- Access to state-of-the-art machinery and technology
- Material sourcing and heat treatment expertise
- Prototyping and testing services
- Rapid turnaround times for mold fabrication and modifications
Future Trends in Injection Mold Tool Design
Looking ahead, the field is poised for continuous innovation, driven by technological advancements and evolving manufacturing demands. Here are some emerging trends:
Smart Mold Technology
Embedding sensors in molds to monitor temperature, pressure, and wear in real-time enables predictive maintenance and enhances process control.
Eco-friendly and Sustainable Practices
Developing molds with recyclable materials and integrating energy-saving manufacturing techniques align with global sustainability goals.
Artificial Intelligence and Machine Learning
AI-driven design optimization processes can predict potential issues and suggest improvements, significantly reducing iterative testing and accelerating development cycles.
Concluding Remarks: The Crucial Role of Advanced Injection Mold Tool Design in Manufacturing Success
In summary, injection mold tool design is a sophisticated discipline that combines engineering mastery, material science, and innovative technology. By leveraging the latest design strategies, high-performance materials, and collaborative expertise from top metal fabricators, manufacturers can produce molds that deliver superior quality, longevity, and cost efficiency.
As the industry continues to evolve, staying at the forefront of these trends will empower your business to achieve a competitive edge. Whether developing complex consumer products, automotive components, or medical devices, mastery of injection mold tool design is essential for success in the modern manufacturing landscape.
To explore tailored solutions for your specific needs, consider partnering with expert metal fabricators like deepmould.net. Their comprehensive services and proven track record make them a trusted partner in the pursuit of excellence in injection mold design.