Custom Mold Makers: The Art and Science Behind Precision Manufacturing
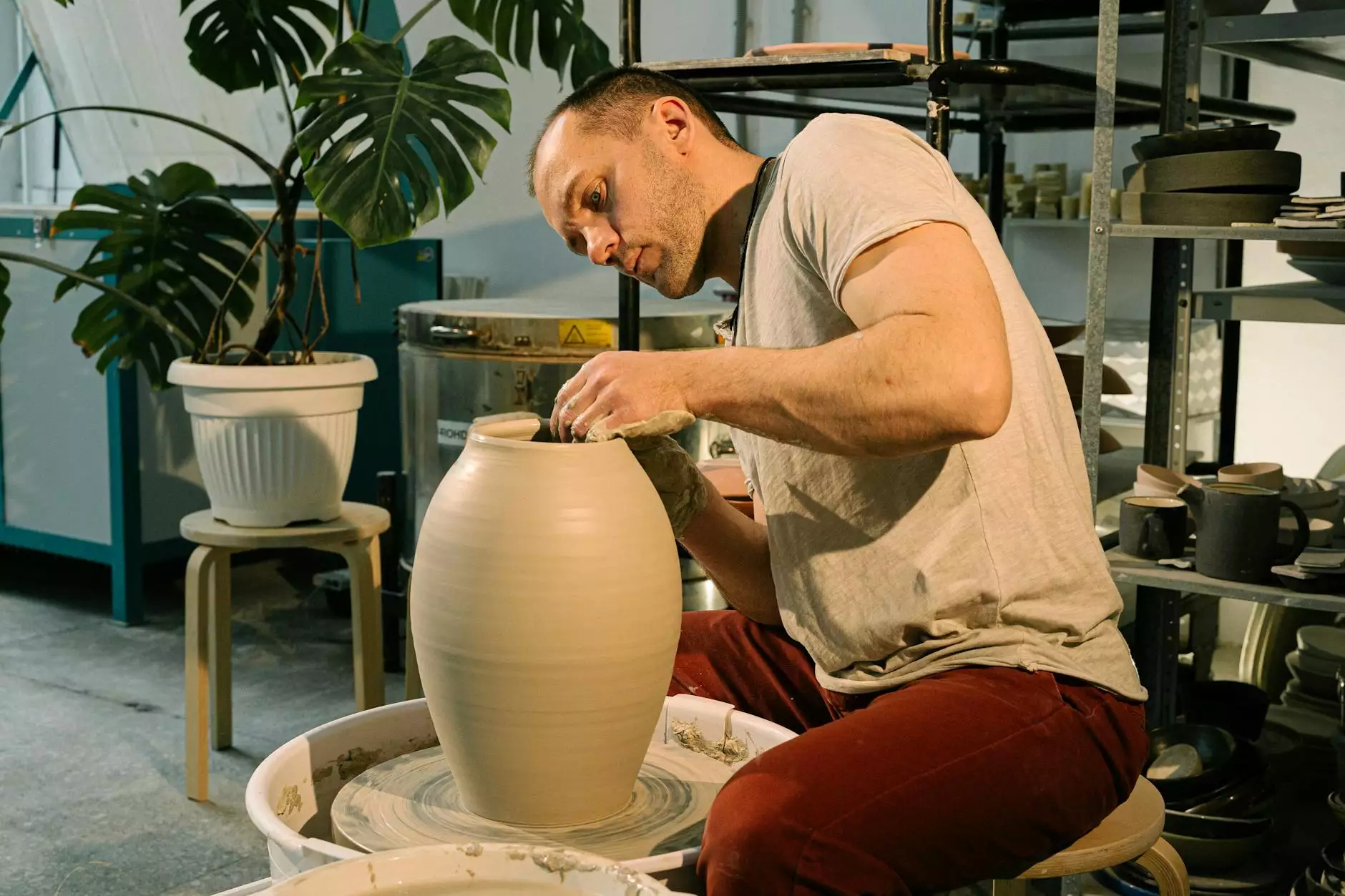
In the world of manufacturing, precision is key. Among the many professionals who contribute to this precision, custom mold makers stand out as essential players. They are the artisans who design and build molds that form the backbone of various production processes. In this comprehensive article, we will explore the vital role of custom mold makers, their processes, the benefits they offer, and their impact on industries like metal fabrication.
Understanding the Role of Custom Mold Makers
Custom mold makers are specialized craftsmen who produce molds used in manufacturing processes. These molds can be made from various materials, including metals, plastics, and ceramics, and they are used in various applications, including injection molding, casting, and machining.
Their primary responsibilities include:
- Designing molds based on specifications provided by clients.
- Using advanced technology and software to create detailed mold designs.
- Fabricating the molds using techniques such as CNC machining and EDM (Electrical Discharge Machining).
- Testing and refining molds to ensure they meet quality standards.
The Importance of Custom Mold Makers in Metal Fabrication
In the realm of metal fabricators, custom mold makers play an indispensable role. They contribute significantly by ensuring that the molds used in the fabrication process are of the highest quality. The metal fabrication industry relies heavily on bespoke molds to produce complex parts with precision and consistency.
Key Benefits of Using Custom Mold Makers
Engaging skilled custom mold makers brings various benefits to businesses involved in metal fabrication and other sectors:
- Enhanced Precision: Custom molds are designed specifically for the required application, ensuring that every part produced meets strict dimensional tolerances.
- Increased Efficiency: High-quality molds help streamline production processes, reducing material waste and increasing throughput.
- Cost-effectiveness: Although the initial investment in custom molds might be higher, the long-term savings achieved through reduced cycle times and waste make them a favorable investment.
- Flexibility: Custom mold makers can create molds that are adaptable to various production volumes, accommodating both low and high runs efficiently.
Processes of Custom Mold Making
The journey from concept to finished mold is intricate and involves several steps that require both creativity and technical expertise:
1. Concept and Design
The process begins with idealizing the mold. Custom mold makers collaborate closely with clients to understand their specific needs, including part designs, material properties, and production goals. Using sophisticated CAD (Computer-Aided Design) software, they create detailed blueprints of the mold.
2. Material Selection
The choice of material for mold making is crucial. Depending on the application, custom mold makers may choose from various materials such as:
- Steel: Known for its strength and longevity.
- Aluminum: Lighter and typically used for lower-volume production.
- Plastics and Composites: Often used for specialized applications.
3. Manufacturing the Mold
Once the design and materials are finalized, the actual manufacturing of the mold begins. Techniques employed by custom mold makers include:
- CNC Machining: Utilizes computer-controlled machines to precisely cut and shape the mold components.
- EDM: Uses electrical discharges to remove material from the mold, allowing for intricate features that are difficult to achieve with traditional machining.
- 3D Printing: Some custom mold makers are now adopting additive manufacturing to create rapid prototypes for testing and evaluation.
4. Testing and Quality Assurance
After the mold is fabricated, it undergoes rigorous testing to ensure it operates correctly during the manufacturing process. This may include:
- Trial runs to evaluate performance.
- Dimensional inspections to confirm accuracy.
- Adjustments and refinements to optimize mold performance.
The Future of Custom Mold Making
The landscape for custom mold makers is changing rapidly due to advancements in technology. Here are some trends shaping the future:
Advancements in Technology
Emerging technologies such as 3D printing, AI and machine learning, and smart manufacturing are revolutionizing mold making. These innovations are leading to faster prototyping, enhanced precision, and greater flexibility in design.
Sustainability Practices
As industries move towards more sustainable practices, so do custom mold makers. The use of eco-friendly materials and processes that minimize waste is becoming increasingly important.
Choosing the Right Custom Mold Maker
When selecting a custom mold maker, it's vital to consider several factors to ensure a successful partnership:
Experience and Expertise
Look for custom mold makers with a proven track record and expertise in your specific industry. Their experience will be invaluable in overcoming challenges during the mold design and manufacturing process.
Technology and Equipment
Evaluate the technology and equipment used by potential mold makers. Up-to-date machinery and design software can significantly improve the quality and efficiency of the mold manufacturing process.
Customer Support and Communication
Effective communication is critical in ensuring that your needs are met. Look for mold makers who prioritize customer support and are willing to engage with you throughout the project.
Conclusion
In summary, custom mold makers are vital to any manufacturing process, especially in the field of metal fabrication. By providing precision tools that enable high-quality production, they help businesses reduce costs, improve efficiency, and innovate their offerings. As technology continues to advance, the role of custom mold makers will only grow, paving the way for even more sophisticated and efficient manufacturing processes.
For businesses looking to thrive in today's competitive landscape, partnering with experienced custom mold makers like those at DeepMould.net can make all the difference in achieving outstanding results and maintaining a competitive edge.